机构中心
行业信息
专业书刊
橡塑装备
- 优质产品
- 创新产品
- 橡胶装备
- 塑料装备
- 配套设备与产品
- 橡塑节能环保装备
- 橡塑制品
- 橡塑工程
人物专栏
终身成就
- 薛志文先生——2020年“终身成就”获得者
- 王洪训先生——2020年“终身成就”获得者
- 陈元荣先生——2020年“终身成就”获得者
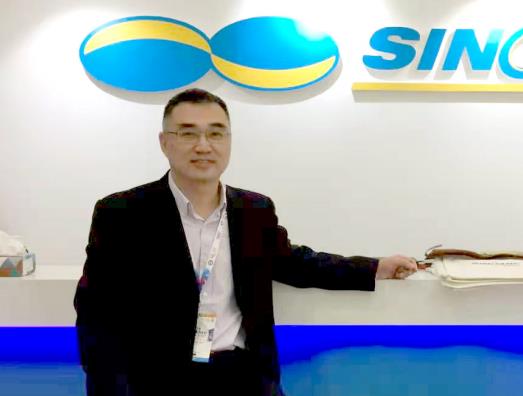
张正罗先生——2020年“终身成就”获得者
张正罗
总工程师/高级工程师
华澳轮胎设备科技(苏州)股份有限公司
1964年7月出生
从事橡机行业工作35年
主要业绩:
张正罗同志 1985 年进入橡胶机械行业,35 年来,一直从事橡胶机械的技术研究和新产品的开发工作。他近年来在轮胎硫化机可靠性技术研究、新产品开发方面成果显著,建立健全了一套激励与约束相结合的研发创新体系,打造出一支有精湛技术水 平,有丰富经验,能够灵活应对国内外市场的高素质国际化创新团队。
多年来,凭借对轮胎技术的专研,以及对橡胶机械行业的执着,主持完成轮胎硫化机、冷喂料销钉挤出机、注塑机等几十项新产品的研究和技术攻关,共申请专利 50 多项,已获授权 41 项,其中发明专利 20 项,最具代表性的“无托板自适应调模的液压式轮胎硫化机”整机专利在美国、日本、德国、俄罗斯等多个国家申请了 PCT 发明专利,在美国、日本、 俄罗斯、泰国、印尼 5个国家已获授权,从知识产权上,与西方先进同行站在同一起跑线上,大大提高国内硫化机的整体水平。
他主持研发的拉杆锁模式液压轮胎硫化机,属于当前国际最新的立柱式机型,该产品被认定为江苏省高新技术产品,为公司成功进入全球知名轮胎制造商的供应体系做出重大贡献;他主持研发的华澳科技第四代液压硫化机(GENIV)得到国内外著名轮胎公司的高度认可,显著提高了华澳公司的市场竞争能力,为华澳公司获得全球轮胎设备行业“年度供应商提名”做出重大贡献。
获奖情况:
2011-2017年,主持开发的拉杆锁模式液压硫化机、无托板自适应调模的液压轮胎硫化机、开合模油缸倒置式液压轮胎硫化机、热板平移式工程胎硫化机、锁模杠杆驱动液压式硫化机等5项产品荣获江苏省高新技术产品;
2018 年,获苏州市优秀专利奖;
2019 年,被选聘为江苏省第七批产业教授。
杰出人物
- 戴造成——第二届中国橡胶机械行业杰出人物
- 方 晓——第二届中国橡胶机械行业杰出人物
- 韩富城——第二届中国橡胶机械行业杰出人物
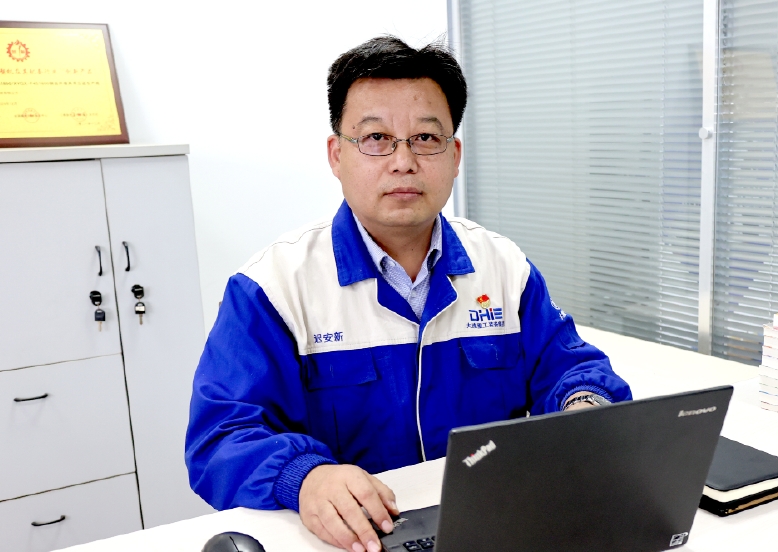
迟安新——第二届中国橡胶机械行业杰出人物
迟安新副总经理/高级工程师大连橡胶塑料机械有限公司1973年8月出生从事橡机行业工作28年 迟安新同志自1996年参加工作以来,从基层做起,认真积极,在橡胶机械领域深耕细作已有28年,他工作经验丰富,工作成绩突出。迟安新同志负责了多个橡胶机械项目的设计和管理工作,包括XMN-320×(5~50)Y啮合型密闭式炼胶机、φ900*2800纤维压延机、串联密炼机和钢纤两用压延机等。其中,XMN-320×(5~50)Y啮合型密闭式炼胶机项目获得了中国机械工业科学技术三等奖,并实现了7000万元的销售收入。 迟安新同志将工作成果总结,发表了多篇论文,对企业的现有产品和新产品开发产生了积极影响。此外,他还参与了多项专利的研发,如同步调整胶片贴合装置、加料门两侧密封结构、密炼机新型压料装置和密炼机的端面密封装置通水冷却结构等,这些专利技术的应用提高了工作效率和设备性能。在多年的职业生涯中,迟安新同志始终坚持以科技创新为核心,不断提升自身专业素养。他的努力不仅为公司带来了丰硕的成果,也为整个橡胶机械行业树立了榜样。获奖情况:2016年获得中国机械工业科学技术三等奖。
时代精英
- 陈 杰——第四届中国橡胶机械行业时代精英
- 陈晓军——第四届中国橡胶机械行业时代精英
- 丁振堂——第四届中国橡胶机械行业时代精英
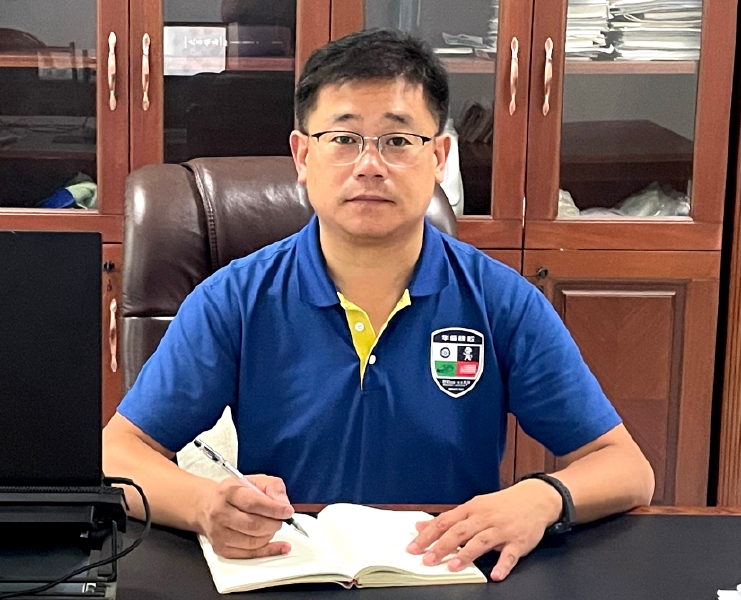
陈建军——第四届中国橡胶机械行业时代精英
陈建军研发中心副主任兼材料研发总监/高级工程师山东华盛橡胶有限公司1977年9月出生从事橡机行业工作24年主要业绩: 陈建军同志自从参加工作以来,专注于半钢轮胎、全钢轮胎以及工程轮胎的配方和材料研发工作,积累了丰富的经验和深厚的专业知识。 陈建军同志的主要工作成就涵盖了推广再生胶的循环利用,显著提升了橡胶资源的回收利用率;研发了用于成型胶囊的配方,有效提高了胶囊的使用次数;研究并提升了载重子午线轮胎的耐久性能;开发了橡胶连续混炼系统;推动了国产SSBR的产业化;研制了PCR四季轮胎;开发了“B、A”标签等级的轮胎产品;研制了高附加值的SUV系列产品;他还主持了雪地轮胎的研制工作;带领技术研发中心通过了多项认定和认证;研制开发了轿车、SUV缺气保用轮胎产品;并且在全热熔赛事轮胎产业中取得了突破。 陈建军同志不仅在技术研发方面取得了显著的成就,还成功主持并承担了六项市级及以上级别的研发项目,他的研究成果为行业的发展作出了重要贡献。陈建军同志发表了超过40篇学术论文,拥有8项有效专利,其中包括4项发明专利和4项实用新型专利,以及2项软件著作权,并参与制定了六项橡胶行业国家技术标准。获奖情况:2006年,荣获“行业优秀工程师”称号;2011年,获得东营市人民政府颁发的科学技术一等奖;2014年,获青岛市科技局的授予“科技进步一等奖”;2015年,荣获“优秀科技工作者”称号;2016年,被青岛市黄岛区人民政府评选授予“科技进步二等奖”;2020年,获得省级技术创新成果一等奖,同时获得省级技术创新优秀论文一等奖。
工匠人物
- 何光发——首届中国橡胶机械行业工匠人物
- 胡 晓——首届中国橡胶机械行业工匠人物
- 蒋海龙——首届中国橡胶机械行业工匠人物
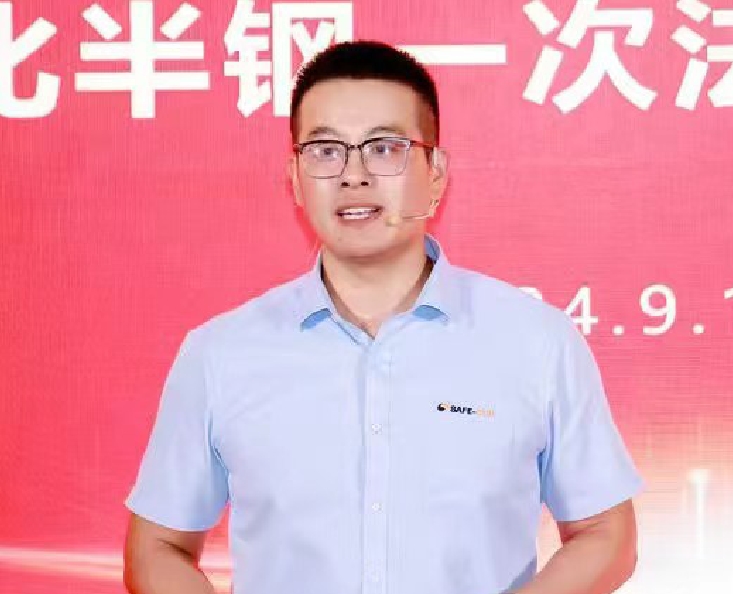
陈如峰——首届中国橡胶机械行业工匠人物
陈如峰轮胎装备中心副总经理萨驰智能装备股份有限公司1988年12月出生从事橡机行业工作12年主要业绩: 陈如峰同志拥有12年橡胶机械行业经验,其专长聚焦于半钢成型机的研发技术、工程调试,以及轮胎工艺与应用的深度探索,目前担任萨驰智能装备股份有限公司轮胎装备中心副总经理。陈如峰同志在山东国风橡塑制品有限公司和萨驰智能装备股份有限公司累计工作超过12年,历任电气维修、设备主管、副部长、电气调试工程师等职。在技术研发领域,陈如峰同志全程参与了半钢一次法成型机的研发设计与工程调试工作,不仅为产品的诞生贡献了关键力量,还积极参与了研发标准的制定与修订,确保技术的前瞻性与实用性。此外,他主导了600多台半钢一次法成型机的安装调试工作,并在2023年成功主导了该机型国产化汇川系统的研发设计和工程调试,实现了技术突破。陈如峰同志因其卓越的工作表现,获得了包括苏州特殊人才引进政策在内的多项奖励,并被评为优秀员工、优秀项目经理和杰出贡献奖。获奖情况:被评为公司优秀员工;被评为优秀项目经理;获得公司颁发的杰出贡献奖。