塑件设计是一项系统性、综合性的工程策划。首先要考虑满足使用功能;然后进行材料选择;确定成型方法(尤其要注意塑件的分型、脱模、排气等);最后才是结构尺寸和技术要求的确定,这时还要顾及品质控制和外表造型及工艺性。整个过程要与生产成本和效率紧密地相结合。
2.1 塑件的几何形状结构
塑件主要是根据使用要求进行设计的,由于塑料有其特殊的物理力学性能,因此,设计塑件时必须充分发挥其性能上的优点,避免或补偿其缺点。在满足使用要求的前提下,塑件形状应尽可能地做到简化模具结构,符合成型工艺特点。在设计塑件时必须考虑以下几方面的因素:
(l)塑料的物理力学性能,如强度、刚度、韧性、弹性、吸水性以及对应力的敏感性。
(2)塑料的成型工艺性,如流动性。
(3)塑料形状应有利于充模流动、排气、补缩,同时能适应高效冷却硬化(热塑性塑料制件)或快速受热固化(热固性塑料制件)。
(4)塑件在成型后收缩情况及各向收缩率的差异。
(5)模具的总体结构,特别是抽芯与脱出塑件的复杂程度。
(6)模具零件的形状及其制造工艺。
以上前四条主要是指塑料性能特点,后两条主要是考虑模具结构特点,塑件设计的主要内容包括塑件的形状、尺寸、精度、表面粗糙度、壁厚、斜度,以及塑件上加强肋、支承面、孔、圆角、螺纹、嵌件等的设置。
2.1.1 壁厚
各种塑件,不论是结构件还是板壁,根据使用要求具有一定的厚度,以保证其力学强度。一般地说,在满足力学性能的条件下厚度不宜过厚,不仅可以节约原材料,降低生产成本,而且使塑件在模具内冷却或固化时间缩短提高生产率;其次可避免因过厚易产生的凹陷、缩孔、夹心等质量上的缺陷。但是过薄会使熔融塑料在模具型腔内的流动阻力增大,造成成型困难,相应地给加工设备的能力(如压力、锁模力等)和模具的设计制造提高要求。另外,当厚度和表面积尺寸相悬较大时,会使塑件翘曲,影响质量。
2.1.1.1 制件壁厚的作用
(1)使制件具有确定的结构和一定的强度、刚度,以满足制件的使用要求。
(2)成型时具有良好的流动状态(如壁不能过薄)以及充填和冷却效果(如壁不能太厚)。
(3)合理的壁厚使制件能顺利地从模具中推出。
(4)满足嵌件固定及零件装配等强度的要求。
(5)防止制件翘曲变形。
2.1.1.2 制件壁厚的设计
制件壁厚设计的基本原则——均匀壁厚,即充模、冷却收缩均匀,形状性好,尺寸精度高,生产率高。
(1)在满足制件结构和使用要求的条件下,尽可能采用较小的壁厚。
(2)制件壁厚的设计,要能承受顶出装置等的冲击和振动。
(3)在制件的连接固紧处、嵌件埋入处、塑料熔体在孔窗的汇合(熔接痕)处,要具有足够的厚度。
(4)保证储存、搬运过程中强度所需的壁厚。
(5)满足成型时熔体充模所需壁厚,既要避免充料不足或易烧焦的薄壁,又要避免熔体破裂或易产生凹陷的厚壁。
塑件的壁厚应尽量均匀,壁与壁连接处的厚薄不应相差太大,并且应尽量用圆弧过渡;否则连接处由于冷却收缩得不均匀,产生内应力而使塑件开裂。热塑性塑件的壁厚,常在l~5 mm范围内选取;热固性塑件的壁厚,小件常在1.5~2.5 mm范围内选取,大件常在3~10 mm范围内选取。精密塑件的壁厚可以不受上述范围限制,例如,轻巧的“随身听”壁厚就小于l mm,与幅跨的比例小于1/l00。
此外,壁厚的取值范国还因选用的聚合物而异。对于流动性比较好的材料,如聚乙烯、聚丙烯和聚酰胺等,壁厚可以薄一些,一般塑件可以小于l mm,甚至可达0.6 mm。表2为热塑性塑料制件的壁厚推荐值,表3为热固性塑料制件的壁厚推荐值。
表2 热塑性塑料制件的壁厚推荐值 mm
表3 固定宽度热固性塑料制件的壁厚推荐值 mm
塑料材料 | 最小壁厚 | 小型制件壁厚 | 中型制件壁厚 | 大型制件壁厚 |
尼龙 | 0.45 | 0.76 | 1.5 | 2.4~3.2 |
聚乙烯 | 0.6 | 1.25 | 1.6 | 2.4~3.2 |
聚苯乙烯 | 0.75 | 1.25 | 1.6 | 3.2~5.4 |
高抗冲聚苯乙烯 | 0.75 | 1.25 | 1.6 | 3.2~5.4 |
聚氯乙烯 | 1.2 | 1.6 | 1.8 | 3.2~5.8 |
有机玻璃 | 0.8 | 1.5 | 2.2 | 4.0~6.5 |
聚丙烯 | 0.85 | 1.45 | 1.75 | 2.4~3.2 |
氯化聚醚 | 0.9 | 1.35 | 1.8 | 2.5~3.4 |
聚碳酸酯 | 0.95 | l.80 | 2.3 | 3~4.5 |
聚苯醚 | 1.2 | l.75 | 2.5 | 3.5~6.4 |
醋酸纤维素 | 0.7 | 1.25 | 1.9 | 3.2~4.8 |
乙基纤维素 | 0.9 | 1.25 | l.6 | 2.4~3.2 |
丙烯酸类 | 0.7 | 0.9 | 2.4 | 3.0~6.0 |
聚甲醛 | 0.8 | 1.40 | l.6 | 3.2~5.4 |
聚砜 | 0.85 | 1.80 | 2.3 | 3~4.5 |
塑料 | 最小壁厚 | 推荐壁厚 | 最大壁厚 |
醇酸树脂一玻纤填充 | l.0 | 3.0 | 12.7 |
醇酸树脂一矿物填充 | l.0 | 4.7 | 9.5 |
酞酸二烯丙醋(DAP) | l.0 | 4.7 | 9.5 |
环氧树脂一玻纤填充 | 0.76 | 3.2 | 25.4 |
三聚氰胺甲醛树脂一纤维素填充 | 0.9 | 2.5 | 4.7 |
氨基塑料一纤维填充 | 0.9 | 2.5 | 4.7 |
酚醛塑料(通用型) | 1.3 | 3.0 | 25.4 |
酚醛一棉短纤填充 | 1.3 | 3.0 | 25.4 |
酚醛一玻纤填充 | 0.76 | 2.4 | 19.0 |
酚醛一织物填充 | 1.6 | 4.7 | 9.5 |
酚醛一矿物填充 | 3.0 | 4.7 | 25.4 |
硅酮一玻纤填充 | 1.3 | 3.0 | 6.4 |
聚酯预混物 | 1.0 | 1.8 | 25.4 |
制件的壁厚太大,塑料在模具中需要冷却的时间越长,产品的生产周期也会延长。制件的壁厚太薄,刚性差,不耐压,在脱模、装配、使用中容易发生损伤及变形;另外,壁厚太薄,模腔中流道狭窄,流动阻力加大,造成填充不满,成型困难。壁厚与流程的关系见表4。
表4 壁厚(S)与流程(i)的关系 mm
塑料品种 | 计算公式 |
流动性好(PE,PA等) | S=(+0.5)×0.6 |
流动性中等(PMMAPOM等) | S=(+0.8)×0.7 |
流动性差(PC,PSu)等 | S=(+1.2)×0.9 |
制件的壁厚原则上要求一致。壁厚不均匀,成型时收缩会不均匀,产生缩孔和内部应力,以致发生变形或者开裂。图12所示为底厚改进设计,图13所示为壁厚改进设计。
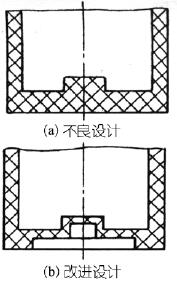
图12 底厚改进设计
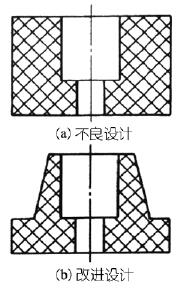
图13 壁厚改进设计
图14所示为采用掏空的方式尽量使壁厚均匀,消除翘曲、凹痕和应力。当不同的壁厚无法避免时,应采用倾斜方式使壁厚逐渐变化,如图15所示。

图14 防止变形的壁厚设计
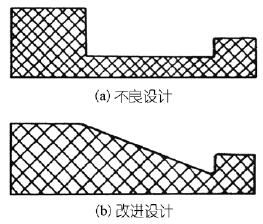
图15 不同壁厚的设计
图16所示为用空心形状来减少塑料质量的设计。图17所示为用掏空方式达到壁厚均匀设计。图18所示为改进圆柱部分壁厚的设计。
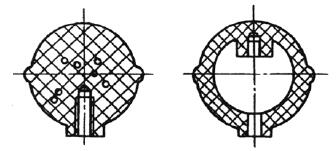
图16 手柄壁厚设计
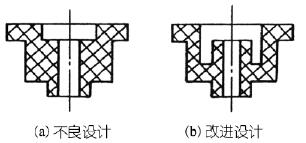
图17 塑料轴承壁厚设计
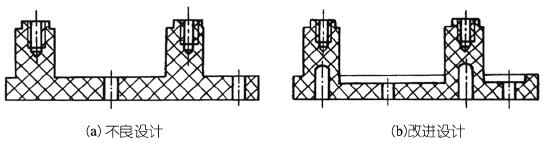
图18 塑件圆柱部分壁厚改进
2.1.2 脱模斜度
由于塑料制件成型时冷却过程中产生收缩。使其紧箍在凸模或成型芯上。为了便于脱模,防止因脱模力过大而拉坏塑件或使其表面受损,与脱模方向平行的塑件内、外表面都应具有合理的斜度,如图19所示。
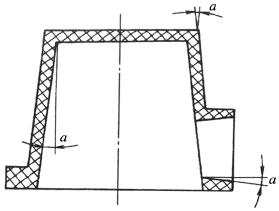
图19 塑件的斜度
脱模斜度的大小与下列因素有关:
(1)制件精度要求越高,脱模斜度应越小。
(2)尺寸大的制件,应采用较小的脱模斜度。
(3)制件形状复杂不易脱模的,应选用较大的斜度。
(4)制件收缩率大,斜度也应加大。
(5)增强塑料宜选大斜度,含有自润滑剂的塑料可用小斜度。
(6)制件壁厚大,斜度也应大。
(7)斜度的方向。内孔以小端为准,满足图样尺寸要求,斜度向扩大方向取得; 外形则以大端为准,满足图样要求,斜度向偏小方向取得。一般情况下,脱模斜度α可不受制件公差带的限制,高精度塑料制件的脱模斜度则应当在公差带内。
脱模斜度α值可按表5、表6选取。
表5 热塑性塑料制件脱模斜度
塑料品种 | 脱模斜度 | |
制件外表面 | 制件内表面 | |
PA(通用) | 20~40' | 25~40' |
PA(增强) | 20~50' | 20~40' |
PE | 20~45' | 25~45' |
PMMA | 30~50' | 35'~1° |
PC | 35~1° | 30'~50' |
PS | 35~1.35° | 30'~1° |
ABS | 40~1.20° | 35'~1° |
表6 热固性塑料制件外表面脱模斜度
制件高度/mm | <10 | 10~30 | >30 |
脱模斜度 | 25~30' | 30~35' | 35~40' |
具备以下条件的型芯,可采用较小的脱模斜度:
(1)推出时制件刚度足够。
(2)制件与模具钢材表面的摩擦因数较低。
(3)型芯的表面粗糙度值小,抛光方向又与制件的脱模方向一致。
(4)制件收缩量小,滑动摩擦力小。
在不影响尺寸精度的情况下,制件的内外表面都应有斜度,特别是深形的容器类制件,制件内侧的斜度可以比外侧的斜度大1°,如图20所示。
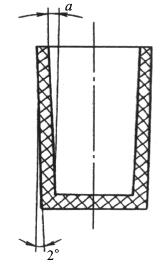
图20 内外表面斜度
当只在制件的内表面有斜度时,制件会留在凹模内,凹模一边应设有推出装置,如图21所示。
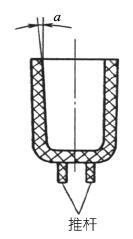
图21 外表面无斜度
箱形或盖状制件的脱模斜度随制件高度略有不同,高度在50 mm以下,取l/30~1/50;高度超过l00 mm,取l/60;在二者之间的取1/30~l/60。格子状制件的脱模斜度与格子部分的面积有关,一般取1/12~l/l4。
2.1.3 加强肋、凸台及支承面
加强肋可定义为塑件上长的突起物,在不增加壁厚的条件下,刚度。凸合是塑件上用来增强孔或供装配附件用的凸起部分,如图22所示。
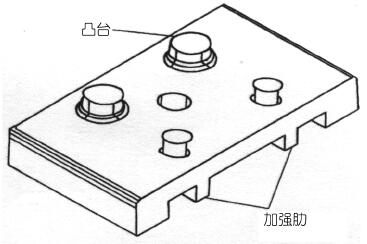
图22 加强肋与凸台
2.1.3.1 加强肋
塑件上适当设置的加强肋可以防止塑件的翘曲变形;沿着物料流动方向的加强肋还能降低充模阻力,提高熔体流动性,避免气泡、缩孔和凹陷等现象的产生。
典型的加强肋形状和比例关系如图23所示。加强肋的高度h≤3t(t为塑件壁厚),脱模斜度α=2~5°。加强肋的顶部应为圆角,底部以半径为R的圆角向周围过渡,R≥0.25t;加强肋宽度b<t,常取b=0.5t。通常,加强肋以高度低(过高时容易在弯曲和冲击负荷作用下受损)、宽度小,而数量多(塑件形状所允许的条件下)为好。图24所示为加强肋宽度,b过宽引起了塑件表面缩瘪缺陷的发生。图25(a)是把大的加强肋改为多条小的加强肋;而图25(b)是把加强肋连结成格子形状。这样,既可提高制件强度,又可防止缩瘪缺陷产生。 加强肋位置的布局应注意以下几点:
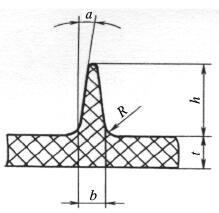
图23 加强肋的结构
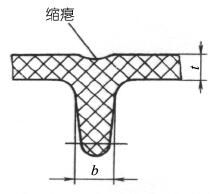
图24 宽加强肋的缩瘪
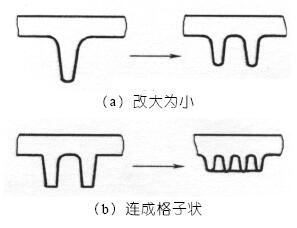
图25 加强肋的防缩瘪措施
(1)加强肋的方向应尽量与物料充模时熔体流动的方向保持一致,以避免因流动受阻出现的成型缺陷或造成塑件的强度和刚度下降。
(2)加强肋应位于制件受力位置上;在有多条肋的情况下,应使各肋的排列互相错开,防止因收缩不均匀而引起的开裂。图26(a)属不合理的布局,会因肋厚集中而出现缩瘪或气泡;宜改为图26(b)所示的布局。

图26 加强肋的布局
(3)较大表面积或外观要求较高的情况下,应避免把加强肋设置在大表面的中部,以防止熔体流动缺陷产生的流纹和凹陷等。为了掩盖凹陷,可在肋所对应的外壁处设置楞沟或流纹,如图27所示。图中的侧向表面,因无楞沟而出现流纹,影响塑件的外观。
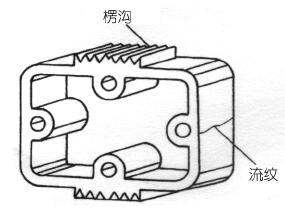
图27 楞沟结构的作用
如图28所示,在长形或深形箱体的转角处设置加强肋,能有效地克服翘曲变形现象。

图28 转角处设置加强肋
加强肋还可起辅助浇道的作用,改善熔体的流动充模状态。图29(a)所示制件强度低,易变形,成型充模困难;图29(b)所示为改进后的状态。
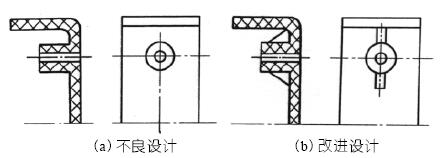
图29 加强肋改善流动的设计
加强肋应设计得低一些、多一些为好。深而狭窄的沟槽会给模具加工带来困难。高而厚会使加强肋所在处的壁厚不均,易形成缩孔和表面凹陷。图30(a)所示虚线处成型会形成表面凹陷,为不良设计;图30(b)为较好的设计。
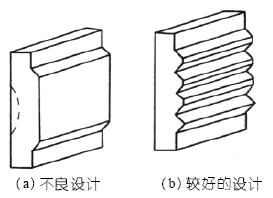
图30 加强肋深浅设计
加强肋的方向应与模压方向或模具的开模方向一致,便于脱模。
另外,还应注意制件的收缩方向,如图31所示。
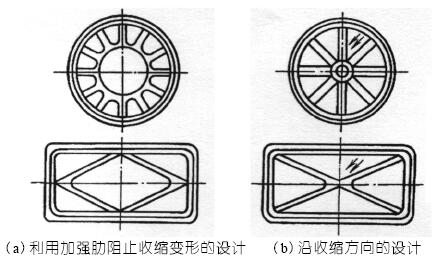
图31 加强肋与收缩方向图
加强肋的端面应低于塑料制件支承面0.5~l mm,如图32所示。
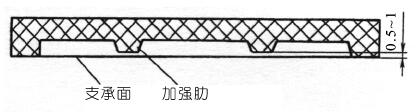
图32 加强肋与支承面
2.1.3.2 凸台
凸台一般位于有加强肋的部位或制件的边缘,如图33所示。凸台处一般能承受较大的推出力,有利于布置推杆。
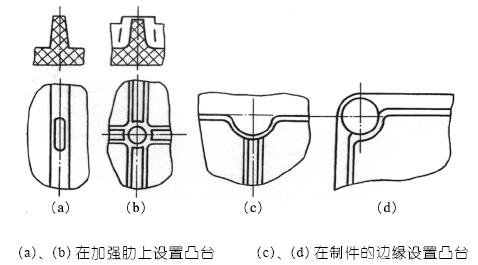
图33 有加强肋时凸台的位置设计
太接近制件的角落或侧壁会增加模具制造的困难,如图34所示。
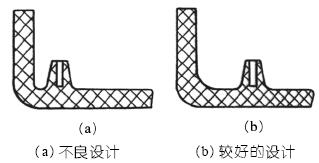
图34 凸台的位置设计
凸台处于平面或远离壁面时,应用加强肋加强,提高其强度并使制件成型容易。
安装紧固凸台的台阶支承面不宜太小,在转折处不要突然变化,应当平缓地过渡,如图35所示。图35(a)为不好的设计,图35(b)为较好的设计。
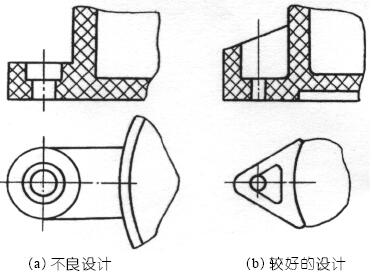
图35 安装紧固凸台的设计
凸台应尽量设计成圆形断面,非圆形断面会增加模具制造的困难,如图36所示。
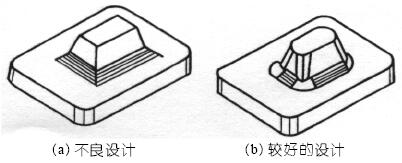
图36 凸台的形状设计
2.1.3.3支承面
以塑件的整个底面作支承面是不合理的,因为塑件稍许翘曲或变形就会使底面不平。常以凸出的底脚(三点或四点)或凸边来作支承面,如图37所示。

图37 用底脚或凸边作支承面
当塑件底部有加强肋时,应使加强肋与支承面相差0.5~1 mm的高度,如图32所示。图38所示为内框支承面。图39所示为支脚支承面。
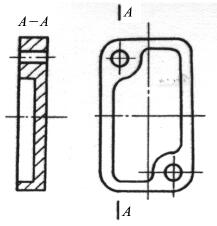
图38 内框支承面
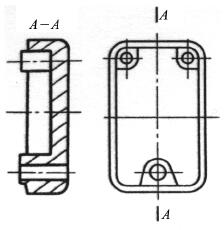
图39 支脚支承面
2.1.3.4其他结构
除了上述的加强肋、度、防止翘曲变形的作用。图40所示的结构使器皿类塑件的边缘增强,实质上是加强肋的变异;图41所示结构使容器底部得以增强;图42所示结构

图40 器皿边缘的增强
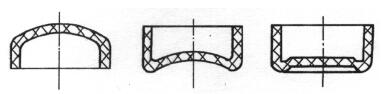
图41 器皿底部的增强
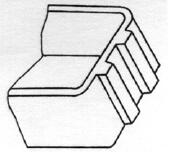
图42 侧壁的增强

图43 预防内凹的方法图
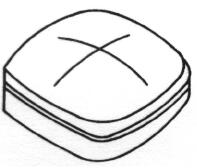
图44 防变形的大抛物
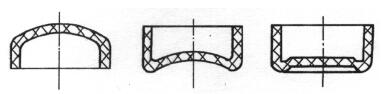
图41 器皿底部的增强
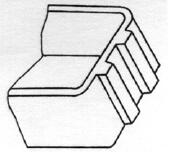
图42 侧壁的增强

图43 预防内凹的方法图
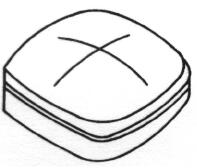
图44 防变形的大抛物
使侧壁增强。有时为了防止软塑料矩形薄壁容器内凹翘曲,而采用预防措施——有意识地先将侧壁设计得稍微外凸,待内凹后恰好平直,如图43所示。这种补偿思维方式能有效地应用于精密塑件的设计,对于不是均匀收缩的塑件,则应考虑在不同部位形态轮廓尺寸上增加或减小某一数值,使成型后的塑件正好在公差范围之内。此外,对于大平面塑件,防止其变形的措施是将形状改为圆弧曲面,若考虑到外观优美,可用抛物面外形,如图44所示。